What measures are taken to prevent cavitation in fire pump impellers and ensure pump efficiency?
Jan 15, 2024
Share:
Cavitation in fire pump impellers can lead to reduced pump efficiency and potential damage to the impeller and other pump components. To prevent cavitation and ensure optimal pump performance, various measures are taken. Here are some common strategies:
1. **Proper Impeller Design:**
- The design of the impeller is crucial in preventing cavitation. Engineers consider factors such as the blade profile, curvature, and geometry to minimize the risk of cavitation. Properly designed impellers help maintain a smooth flow of water through the pump.
2. **Sufficient Net Positive Suction Head (NPSH):**
- Ensuring that the pump system has an adequate Net Positive Suction Head (NPSH) is essential. NPSH is a measure of the absolute pressure at the pump suction. Sufficient NPSH helps prevent the formation of vapor bubbles, which can lead to cavitation.
3. **Submergence and Inlet Conditions:**
- The pump's inlet conditions, including submergence and pipe geometry, are considered during installation. Maintaining proper submergence levels and ensuring a straight, unobstructed flow into the pump inlet helps prevent turbulence and cavitation.
4. **Impeller Material and Coating:**
- The choice of impeller material and coatings can impact cavitation resistance. High-quality materials and coatings that are resistant to erosion and corrosion help maintain impeller integrity and performance.
5. **Pump Speed Control:**
- Controlling the pump speed can be an effective measure to prevent cavitation. Variable Frequency Drives (VFDs) or other speed control mechanisms allow operators to adjust the pump speed based on demand, reducing the risk of cavitation during low-flow conditions.
6. **Regular Maintenance:**
- Regular inspection and maintenance of the pump system are essential to identify and address issues that may contribute to cavitation. This includes checking for wear on impeller blades, inspecting seals, and ensuring proper alignment.
7. **Air and Gas Removal:**
- Proper venting and air removal from the pump system help minimize the presence of air or gases that can contribute to cavitation. Adequate priming and venting procedures are important during pump startup.
8. **Monitoring and Alarming Systems:**
- Installing monitoring systems that can detect cavitation and provide alarms allows operators to take corrective action promptly. Monitoring may involve vibration analysis, acoustic sensors, or other technologies.
9. **Education and Training:**
- Training pump operators and maintenance personnel on the importance of preventing cavitation and the proper operating procedures can contribute to the long-term efficiency and reliability of the fire pump.
10. **System Analysis and Design Review:**
- Conducting a thorough analysis of the entire pump system and reviewing the design parameters can help identify potential cavitation risks. This includes evaluating the pipe layout, valve configurations, and pump placement.
By combining these measures and adopting a proactive approach to maintenance and system design, fire pump operators can minimize the risk of cavitation and ensure the continued efficiency and reliability of their pump systems.
1. **Proper Impeller Design:**
- The design of the impeller is crucial in preventing cavitation. Engineers consider factors such as the blade profile, curvature, and geometry to minimize the risk of cavitation. Properly designed impellers help maintain a smooth flow of water through the pump.
2. **Sufficient Net Positive Suction Head (NPSH):**
- Ensuring that the pump system has an adequate Net Positive Suction Head (NPSH) is essential. NPSH is a measure of the absolute pressure at the pump suction. Sufficient NPSH helps prevent the formation of vapor bubbles, which can lead to cavitation.
3. **Submergence and Inlet Conditions:**
- The pump's inlet conditions, including submergence and pipe geometry, are considered during installation. Maintaining proper submergence levels and ensuring a straight, unobstructed flow into the pump inlet helps prevent turbulence and cavitation.
4. **Impeller Material and Coating:**
- The choice of impeller material and coatings can impact cavitation resistance. High-quality materials and coatings that are resistant to erosion and corrosion help maintain impeller integrity and performance.
5. **Pump Speed Control:**
- Controlling the pump speed can be an effective measure to prevent cavitation. Variable Frequency Drives (VFDs) or other speed control mechanisms allow operators to adjust the pump speed based on demand, reducing the risk of cavitation during low-flow conditions.
6. **Regular Maintenance:**
- Regular inspection and maintenance of the pump system are essential to identify and address issues that may contribute to cavitation. This includes checking for wear on impeller blades, inspecting seals, and ensuring proper alignment.
7. **Air and Gas Removal:**
- Proper venting and air removal from the pump system help minimize the presence of air or gases that can contribute to cavitation. Adequate priming and venting procedures are important during pump startup.
8. **Monitoring and Alarming Systems:**
- Installing monitoring systems that can detect cavitation and provide alarms allows operators to take corrective action promptly. Monitoring may involve vibration analysis, acoustic sensors, or other technologies.
9. **Education and Training:**
- Training pump operators and maintenance personnel on the importance of preventing cavitation and the proper operating procedures can contribute to the long-term efficiency and reliability of the fire pump.
10. **System Analysis and Design Review:**
- Conducting a thorough analysis of the entire pump system and reviewing the design parameters can help identify potential cavitation risks. This includes evaluating the pipe layout, valve configurations, and pump placement.
By combining these measures and adopting a proactive approach to maintenance and system design, fire pump operators can minimize the risk of cavitation and ensure the continued efficiency and reliability of their pump systems.
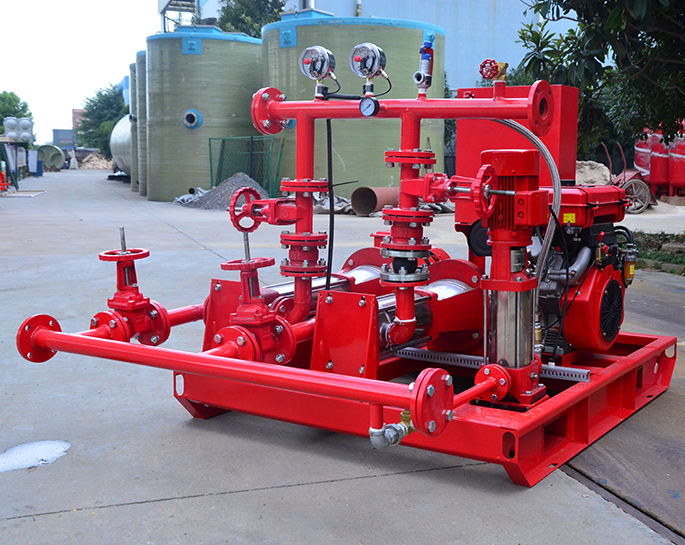