What measures are taken to prevent corrosion in fire pump piping systems?
Jan 03, 2024
Share:
Preventing corrosion in fire pump piping systems is essential to ensure the reliability and effectiveness of the fire suppression system. Corrosion can compromise the integrity of pipes, fittings, and other components, leading to leaks, reduced flow rates, and potential system failures. Here are some measures commonly taken to prevent corrosion in fire pump piping systems:
1. **Material Selection:**
- Choose corrosion-resistant materials for constructing the fire pump piping system. Common materials used include stainless steel, galvanized steel, or materials with corrosion-resistant coatings. The selection of materials should take into account the specific environment, potential corrosive agents, and the type of fire-resistant fluid being used.
2. **Protective Coatings:**
- Apply protective coatings on the interior and exterior surfaces of the pipes and fittings. Corrosion-resistant coatings, such as epoxy coatings, can provide a barrier against corrosive elements. These coatings help prevent the metal surfaces from coming into direct contact with the surrounding environment.
3. **Cathodic Protection:**
- Implement cathodic protection systems to control corrosion. This involves placing sacrificial anodes or using impressed current systems to protect the metal components of the fire pump piping system. Cathodic protection helps divert corrosion away from critical components.
4. **Water Treatment:**
- If the fire pump system uses water as the fire suppression agent, proper water treatment is crucial. Treating the water to control pH levels, minimize dissolved oxygen, and remove impurities can help prevent corrosion in the piping system. Water treatment can include the use of corrosion inhibitors and antifreeze agents.
5. **Regular Inspections and Maintenance:**
- Conduct regular inspections of the fire pump piping system to identify signs of corrosion, such as rust, scale, or pitting. Implement a proactive maintenance program to address any issues promptly. This may involve cleaning, repainting, or replacing corroded components.
6. **Proper Grounding:**
- Ensure proper grounding of the fire pump system. Grounding helps prevent electrolytic corrosion by providing a low-resistance path for electric currents. Corrosion due to stray currents can be minimized by implementing effective grounding techniques.
7. **Dielectric Unions:**
- Install dielectric unions at connections between dissimilar metals. These unions help prevent galvanic corrosion, which occurs when two different metals are in contact and exposed to an electrolyte, such as water. Dielectric unions act as a barrier to the electrical currents that cause galvanic corrosion.
8. **Isolation Devices:**
- Use isolation devices, such as insulating flanges and gaskets, to separate different sections of the piping system. This can prevent the transfer of corrosive agents between sections and reduce the risk of corrosion at connection points.
9. **Corrosion Monitoring:**
- Implement corrosion monitoring systems to assess the condition of the fire pump piping system over time. Monitoring can include the use of corrosion probes, ultrasonic testing, or other inspection methods to detect corrosion early and take corrective actions.
By combining these measures, fire pump system operators can significantly reduce the risk of corrosion in piping systems, ensuring the long-term reliability and performance of the fire suppression system. Regular maintenance and monitoring are crucial components of any corrosion prevention strategy.
1. **Material Selection:**
- Choose corrosion-resistant materials for constructing the fire pump piping system. Common materials used include stainless steel, galvanized steel, or materials with corrosion-resistant coatings. The selection of materials should take into account the specific environment, potential corrosive agents, and the type of fire-resistant fluid being used.
2. **Protective Coatings:**
- Apply protective coatings on the interior and exterior surfaces of the pipes and fittings. Corrosion-resistant coatings, such as epoxy coatings, can provide a barrier against corrosive elements. These coatings help prevent the metal surfaces from coming into direct contact with the surrounding environment.
3. **Cathodic Protection:**
- Implement cathodic protection systems to control corrosion. This involves placing sacrificial anodes or using impressed current systems to protect the metal components of the fire pump piping system. Cathodic protection helps divert corrosion away from critical components.
4. **Water Treatment:**
- If the fire pump system uses water as the fire suppression agent, proper water treatment is crucial. Treating the water to control pH levels, minimize dissolved oxygen, and remove impurities can help prevent corrosion in the piping system. Water treatment can include the use of corrosion inhibitors and antifreeze agents.
5. **Regular Inspections and Maintenance:**
- Conduct regular inspections of the fire pump piping system to identify signs of corrosion, such as rust, scale, or pitting. Implement a proactive maintenance program to address any issues promptly. This may involve cleaning, repainting, or replacing corroded components.
6. **Proper Grounding:**
- Ensure proper grounding of the fire pump system. Grounding helps prevent electrolytic corrosion by providing a low-resistance path for electric currents. Corrosion due to stray currents can be minimized by implementing effective grounding techniques.
7. **Dielectric Unions:**
- Install dielectric unions at connections between dissimilar metals. These unions help prevent galvanic corrosion, which occurs when two different metals are in contact and exposed to an electrolyte, such as water. Dielectric unions act as a barrier to the electrical currents that cause galvanic corrosion.
8. **Isolation Devices:**
- Use isolation devices, such as insulating flanges and gaskets, to separate different sections of the piping system. This can prevent the transfer of corrosive agents between sections and reduce the risk of corrosion at connection points.
9. **Corrosion Monitoring:**
- Implement corrosion monitoring systems to assess the condition of the fire pump piping system over time. Monitoring can include the use of corrosion probes, ultrasonic testing, or other inspection methods to detect corrosion early and take corrective actions.
By combining these measures, fire pump system operators can significantly reduce the risk of corrosion in piping systems, ensuring the long-term reliability and performance of the fire suppression system. Regular maintenance and monitoring are crucial components of any corrosion prevention strategy.
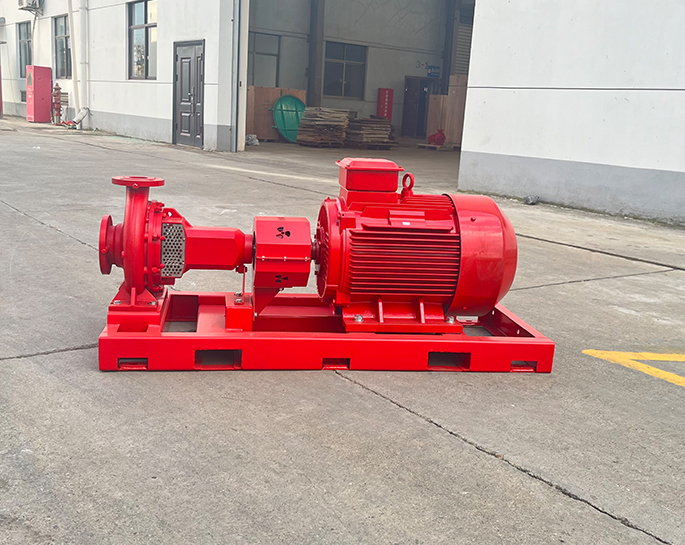